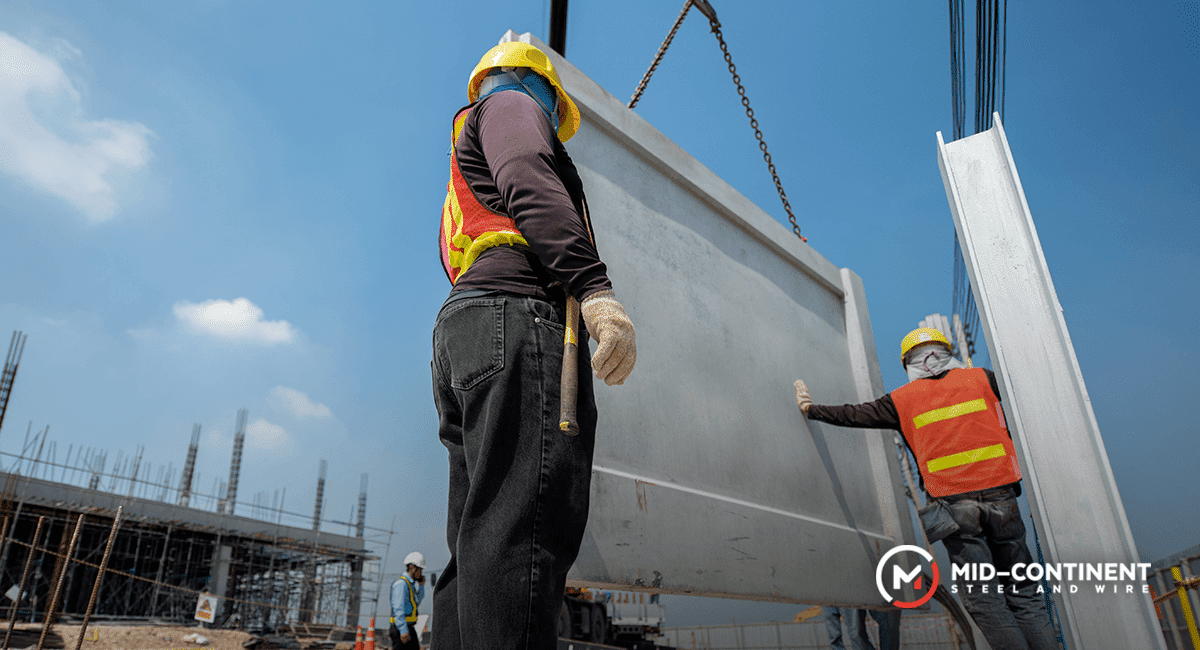
Precast concrete is a type of construction material that is produced by casting concrete in a reusable mold or form off-site and then cured in a controlled environment before being transported to the construction site. This method offers several advantages, including increased efficiency, higher quality control, and reduced construction time.
Keep reading to find out how precast concrete is made.
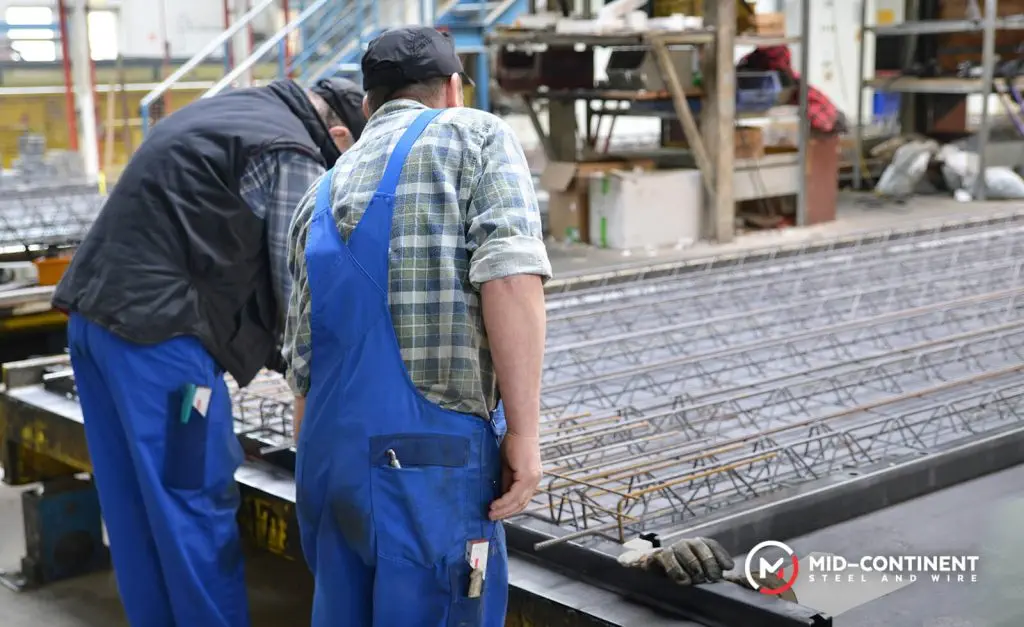
An overview of the process of making precast concrete
The production of precast concrete structures involves several key steps, from design and mold preparation to transportation and installation. Here’s a more detailed breakdown of the process:
- Design and mold preparation: The first step involves designing the precast concrete elements and creating molds or forms to the desired specifications. Molds are typically made of steel or fiberglass and can be reusable for multiple castings.
- Concrete mix design: The mix may include cement, aggregates (such as sand and gravel), water, and admixtures to enhance specific properties of the concrete.
- Batching: The individual components of the concrete mix are precisely measured and mixed in a batching plant. This ensures consistency and quality in the final product.
- Casting: The mixed concrete is poured into the molds, taking the shape of the desired precast element. Reinforcement, such as steel bars or mesh, may be placed within the mold to provide additional strength to the final product.
- Curing: Once the concrete is cast, it undergoes a curing process to develop its strength and durability. Curing is often done in a controlled environment, such as a curing chamber or a water bath, to maintain optimal conditions for hydration.
- Demolding: After the concrete has sufficiently cured, the precast elements are removed from the molds. The molds are then cleaned and prepared for the next casting.
- Finishing: Precast elements may undergo additional finishing processes, such as surface treatments, polishing, or the application of coatings, to achieve the desired appearance and functionality.
- Transportation: Once the precast elements are ready, they are transported to the construction site. Transportation is typically done using specialized vehicles equipped to handle the size and weight of the precast pieces.
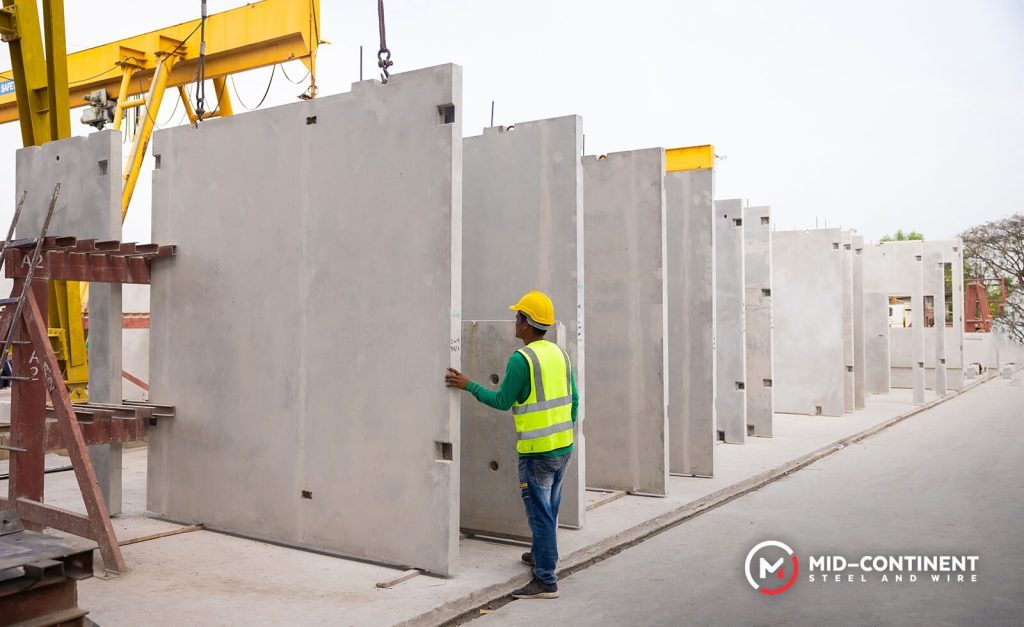
Materials used in precast concrete
The materials used in the precast concrete industry are similar to those used in traditional cast-in-place concrete, but they are carefully selected and controlled to ensure high quality and consistency. The main components of precast concrete include:
- Cement: Cement is a binding agent that reacts with water to form a solid matrix. Portland cement is the most common type used in precast concrete.
- Aggregates: Fine aggregates such as sand provide a smooth texture to the concrete and help fill voids between larger particles. Coarse aggregates like gravel or crushed stone add strength to the concrete and reduce shrinkage.
- Water: Water is crucial for the hydration of cement, leading to the hardening of the concrete mix.
- Admixtures: Plasticizers improve the workability of the concrete mix, making it easier to handle and place. Retarders slow down the setting time of the concrete, which can be beneficial for transportation and casting processes. Accelerators speed up the setting time, which can be useful in cold weather conditions.
- Reinforcement: Steel bars or mesh are often added to precast concrete elements to enhance their structural integrity and resistance to tension forces.
The proportions of these ingredients in the concrete mix are carefully controlled to achieve the desired strength, durability, and other properties. The mix design is an essential aspect of precast concrete production, and it is adjusted based on factors such as the intended use of the concrete, environmental conditions, and specific project requirements.
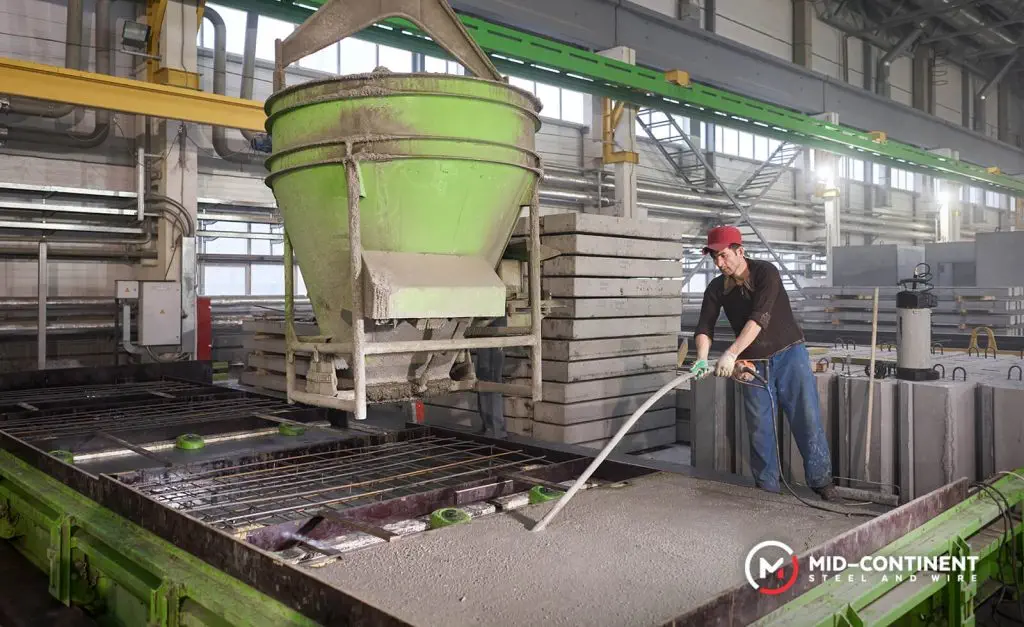
Precast concrete building is an off-site process
Precast concrete construction benefits from a controlled environment away from the construction site. This is in contrast to traditional cast-in-place concrete, where the concrete is poured, formed, and cured on-site. Here’s a breakdown of why precast concrete is typically produced off-site:
- Controlled Environment: Off-site production allows for better control of environmental factors such as temperature, humidity, and curing conditions. This control contributes to consistent and high-quality concrete.
- Quality Assurance: In a controlled factory setting, manufacturers can implement rigorous quality control measures throughout the production process, ensuring that each precast element meets the specified standards and requirements.
- Efficiency and Speed: Precast concrete production can occur concurrently with site preparation and foundation work. This parallel processing can significantly reduce overall construction time.
- Reduced On-Site Disruptions: Since precast elements are manufactured off-site, on-site construction activities are less disruptive, reducing noise, dust, and other inconveniences for surrounding areas.
- Cost Savings: Off-site production can lead to cost savings by optimizing resources, minimizing waste, and improving overall efficiency in the manufacturing process.
- Customization: Precast concrete allows for a high degree of customization in terms of shape, size, and finish. Off-site production facilitates the implementation of specialized molds and finishing processes to achieve the desired aesthetics and functionality.
- Consistency: The controlled conditions of a precast concrete facility contribute to consistent curing, resulting in uniform strength and durability across all precast elements.
- Flexibility: Precast elements can be produced in advance and stored until needed, allowing for flexibility in construction scheduling and adaptability to changing project timelines.
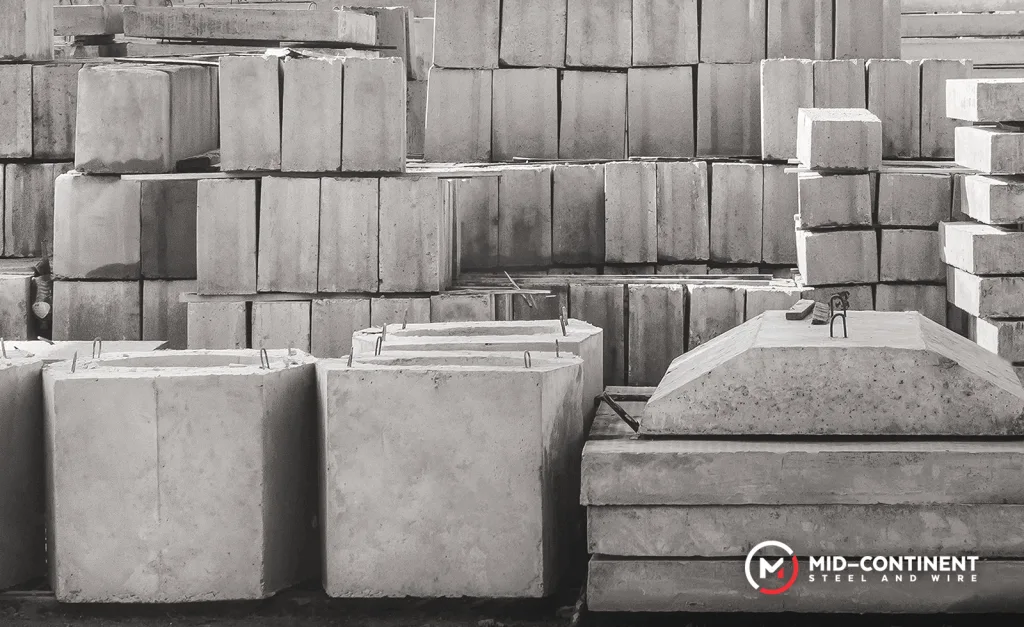
Mid-Continent has everything you need for your precast concrete forming systems
We carry a broad mix of wire mesh products for use in precast concrete building components. From Welded Wire Reinforcement Mesh for concrete reinforcement to Wire Fence and Netting products for different uses and projects. We also offer Fibers as reinforcing steel in concrete structures.
Our Welded Wire Reinforcement Mesh is designed for reinforcing concrete to be used in combination and/or as a substitute to using rebar, which mostly requires manual placement.
We also manufacture gabions adaptable to unstable soil conditions, they are flexible, durable, and resistant to weather conditions.
We also offer furred and non-furred Stucco Netting and steel fibers. If you’re interested in building solid foundations for your projects, don’t hesitate to get in touch with us.